Casting is one of the methods of metal shaping, aside from welding, stamping, forging, extrusion, as well as machining. There are many distinct casting techniques, each of which necessitates slight variations. The classification of the distinct types of casting processes is based on the material, used to manufacture molds. The different casting options comprise sand casting, shell molding, plaster casting, wax casting, centrifugal casting, and die casting. While each casting technique creates distinctive challenges as well as process enhancements, all of them retain the exact basic steps.
Pattern Making
To make a casting mold, a physical model has to be designed first by the manufacturer. The process of fabricating it is known as pattern making. With CAD system, manufacturer designs a mold’s dimensions as well as geometry, and packs an aggregate material, like sand, plastic or concrete, around its pattern. Once it is removed, mold cavity in sand can be filled.
Core Making
Several component designs necessitate the cores’ inclusion in the mold. They are solid materials put within the mold cavity in order to make casting’s interior surfaces. For instance, a metal pipe fitting will necessitate a cylindrical core within the cavity in order to make the part interior’s hollow construction.
Molding
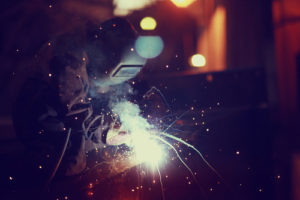
Metal Casting Process
At this point, the casting mold can be created. A material like plaster, sand, or wax is used in expendable mold casting, while metal and other long-lasting materials are employed in non-expendable variants of the technique. It fills the model of the casting mold and is allowed to solidify, at which point the material is removed from the cavity, and casting of the part can then start.
Melting and Pouring
The metal should be melted before being poured into the mold. Usually, it is done with crucibles. They are containers made of a melt-resistant substance wherein the operator can heat a component metal beyond the melting point. Once it is melted, it is poured into mold to cool and solidify.
Finishing
Since metal can at times fill in a casting mold or sprue cracks, the manufacturer should often finish the metal after casting. It can be done using an array of finishing methods, comprising grinding, sanding, and buffing. Once a proper form and surface texture of the component has been achieved, post-treatment methods like electroplating or painting may be required for some applications.