Once you speak to your design and engineering team to decide what type of surface finish you will utilize, the next significant thing to consider is process control. The performance of the surface finish you select will be dependant in part upon the casting or substrate’s quality. What top die casters have found is that there are important process parameters that have to be monitored during the metallurgical process. When you eventually collaborate with a company that provides die casting in Los Angeles or elsewhere, you need to have a talk with it matters regarding how it plans to monitor those parameters. That is important because if it has control of the process and is appropriately monitoring it, then engineers are manufacturing quality into a component.
It is fair to say a die casting project starts with a tool design, based upon the component manufacturability. Therefore, you have to get your die casting company involved early on in the process so that the component is properly designed, and mold flow analysis tested to make sure that your tool is properly constructed. The construction of tool comes into play on a substrate casting’s surface condition.
What is E-Coat?
There are many distinct surface finishing techniques out there, and one of them is the e-coat process. It is described as a racked process, so you are adding a bit more expenditure in the racking as well as un-racking process. Although, you still get great coverage with the e-coat finish. Often, it is used on its own. However, it can be used also as a component’s undercoat for subsequent coating such as a powder coat. The e-coat finish can be exerted to almost any material, such as zinc, aluminum, steel, magnesium, and more. It is an extremely robust finish.
What is Physical Vapor Deposition?
Abbreviated PVD, it is a batch process wherein there is a controlled explosion, and target metal is being vaporized and then transferred to a component’s surface. In order to use PVD, the component should be firstly chrome-plated, and liquid inside it should be removed. The process is extremely expensive but has plenty of distinct colors available. The physical properties of it are tremendous, very durable too, but the whole thing has to be correct to avoid damaged components and get the preferred effect.
What is the Ideal Pretreatment for Preparing Aluminum Castings?
Shot blasting the castings before finish is provided with is the most common approach. E-coating process would be an ideal economical operation. Another surface treatment is chemical film. It acts a primer, excellent for wet coat finish on aluminum material.
What Do the Term “Salt Spray Hours” Imply in Real-World Applications?
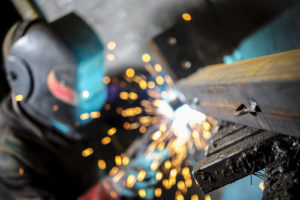
Die Casting Facts
Little evidence is there suggesting a positive correlation of the said hours to what is going to occur to any given component over a specific time period in the real world. Usually, with automotive interior components, you are looking at about forty-eight hours. However, for an exterior application in service condition, the time can be up to 1000 hours. Copper accelerated acetic acid salt spray is something, which simulates a longer use in a short time period. It is distinct to natural salt spray.
How Much Component Material is Removed or Lost during Shot Blast Process?
During the said process, a component’s surface is actually preened off, so no material is lost or removed. The process is used usually to soften parting lines or get rid of any sharp edges, which could affect assembly line workers involved in the process. Besides, it can be used to provide a component with uniform finish.
Is Black Plating Distinct than Chrome Plating?
The answer to that is a No, of course. That is because chemical companies have actually come up with an array of ways and chemicals to produce what would be otherwise the usual shiny chrome finish into black nickel or black chrome. With chrome plating, you can get the black chrome appearance. You can get other colors too, like an indigo chrome, but not all chrome plating offers colored or black chrome. As a result, it is usually more costly than bright chrome.
How Do E-Coats Differ to Powder Coating?
While e-coating process is described as a dip process, powder coating is called a spray process. The former is more fluid in comparison, and is able to reach all pockets and corners of a component, subjected to e-coating process. With it, the full rack is dipped. On the other hand, a rack design as well as placement is important more on a powder coat in order to make sure equal coverage on a component’s all sides. Oftentimes, particularly in case it is an exterior application, a component will be subjected to e-coat and then a powder coat.