The zinc material can be used in many manufacturing sectors, comprising the branch of appliances. The benefits of the use of the material for the manufacturing of small appliances’ parts, specifically those of coffee machines, are as follows.
Design Freedom
Zinc or ZAMAK alloys, lets the manufacturing of parts having just about any type of shape. Owing to the material, it is possible to get extremely thin surfaces of components that could not be attained with other materials, like aluminum. This gives more freedom in component design, with consequent distinctiveness and uniqueness of the manufactured piece. Therefore, zinc presents an excellent metal for the production of parts, which turn out to be intricate from a shape point of view.
By selecting zinc for the manufacturing of small appliances, it is possible to accomplish many benefits related to the components’ quality, since zinc alloys offer stable shrinking as well as high resistance. For instance, as opposed to plastic materials, it offers a superior typical precision as well as better yield and tensile strength. These attributes result in superior freedom of part design, not to mention an end product’s remarkable qualities.
High-End Aesthetical Treatments
Many superficial component treatments can be exerted on zinc alloys. It is particularly possible to improve components’ aesthetical characteristics through treatments that transform them and enhance their finish. The main treatments achievable on zinc are as follows:
- Galvanic treatments namely satin chrome finish, polished chrome finish, and different colors finish
- Powder coating
- Liquid painting
- Special treatments in order to avoid material’s wear
In addition, specific surface treatments taking advantage of the alloy’s physical properties can be achieved on zinc parts. Among the above-mentioned treatments, the second one is a fine example of one that is realizable through powder electrode position as well as heating at high temperatures (about 200 degrees Celsius). This type of coating allows getting a superior texture to touch as opposed to painting. Achieving this treatment for zinc on a part lends a significant added value to it.
Customer Experience
The customer experience is another aspect, which has to be considered when choosing a material. The relationship between end users and a product consists of many variables, like performance as well as usefulness, but also its visual appearance, texture as well as durability. Zinc parts result in excellent customer perceptions with regard to visual impact as well as touch feeling. A component made of it is likelier to be perceived by them as clean, resistant as well as of high quality.
With regard to these features, it is necessary to take into account end users have access to small appliances’ use through buttons and handles. In case a product’s body is made of plastic, its button or handle should be made of zinc to offer its user a different experience. These details improve customer’s experience as well as make the difference in their product choice.
Cleaning of Parts
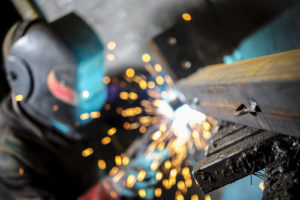
Zinc Die Casting
From the perspective of its end user, the ease of cleaning is one of the aspects that influence the product buying choice. For instance, cleaning chromed zinc parts is easier as opposed to other surfaces since they offer a hard, solid as well as smooth surface. A product that has these characteristics makes the cleaning process faster and more efficient, which is another advantage for end users. Besides being easy to clean, chromed zinc components also convey a perception in them of neatness as well as brightness. These qualities make the parts stand out as opposed to other surfaces.
The Recyclability of Zinc
More and more companies are looking for sustainability these days. To support sustainable development, it is advisable to use materials that are recyclable. Zinc alloys can be melted and used many times over without detriment to the properties of them. Usually, remelted zinc alloys’ use is restricted to around fifty percent and this allows to fully exhaust manufacturing scrap.
Nowadays, the implementation of this system of recycling allows recycling a large number of die casting scraps. Zinc, therefore, presents material with extremely low toxicity, and one that is not energy intensive to manufacture and recyclable. These zinc properties make it an environmentally friendly material.
Reduced Lead Time
This refers to the time a company requires to fulfill the market or customer request with regards to product supply. Logically, a short time period translates to quicker outputs and a satisfied client. To achieve this condition, zinc offers an efficient material owing to its decreased cycle time. In fact, it is a concept that is related to cycle time, the time period necessitated to finish a product’s manufacturing, comprising every process that leads to a finished product. Considering a product’s cycle time, it is thus possible to assume the related lead time of it. By selecting zinc in place of other materials, like plastic and aluminum, lead time will be reduced, resulting in a quicker and more efficient service.
Cycle times that are related to zinc alloys’ die casting are lower as opposed to those of aluminum alloys as well as plastic materials. In aluminum die casting, the material is molded at significantly higher temperatures, thus its cycle time is better owing to cooling range. Plastic has better filling times.