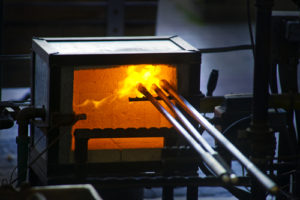
Plunger Lubricants Benefits
The plunger is a rod or piston used to inject molten metal into the die cavity during high-pressure die casting. The use of this rod helps in forcefully inject the molten metal at the right speed and pressure into the die cavity. Thus, plunger plays a pivotal role in die casting to ensure that the dies get inserted into the cavity for ensuring proper quality in the casted components. While using the plunger, it is important to lubricate it so that it helps in smoothly inserting the die into the cavity without relying on excessive force.
A properly lubricated plunger can also aid in considerably minimizing the overall energy consumed during the die casting process. It can even prevent early wear and tear of the plunger tip, thus extending its lifespan. This can also save the costs at the end that comes with replacing the plunger tip from time to time. What lubrication does is it makes a protective coating around the plunger so that it is shielded from the molten metal and prevents its entry beside the tip.
This will prevent any problems that arise due to the molten metal leakage that can make it difficult to operate the plunger. The use of proper plunger lubricants can help in facilitating a smooth sliding motion when the molten metal is injected into the cavity. However, it is important to use the right kind of lubricants for lubricating the plunger. This is because plungers can also contribute to the development of porosity in the casted components that can severely affect its quality.
Lubricants are mostly water based and the presence of such soluble components on the die can result in the development of porosity in the die. The lubricants used on a plunger can also result in them to get in contact with the die thus increasing the chance of increasing the amount of porosity in the castings. Besides, the plunger lubricants can also result in the formation of various discolorations on the casting surfaces.
Such issues are mostly because of the use of low-quality plunger lubricants or the excessive application of them. The use of quality plunger lubricants is thus necessary to help in increasing the efficiency of the die casting process and to minimize any defects arising due to porosity or discoloration of the casted components. The use of solid, oil-based or wax type plunger lubricants can help in enhancing the die casting process and decrease the probability of such common defects.