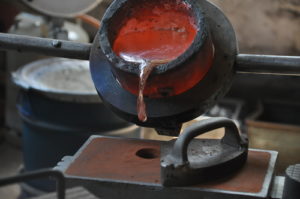
Zinc Plating Processes
Engineers electroplate zinc coatings on a ferrous metal surface in order to create a barrier, which would avoid substrate corrosion. Zinc provides an affordable means of corrosion resistance for ferrous metals and is popularly used in an array of manufacturing methods. In fact, everything from bolts, nuts, and automobile parts to a plethora of consumer goods are zinc coated these days.
Zinc can form adherent byproducts, often referred to as zinc patina, which can drastically reduce the rate of corrosion of ferrous metals to other types of ferrous materials. They are meant to serve as a barrier, which protects corrosion on metal surfaces by keeping out moisture that can increase corrosion process. Besides, as per the state of the environment, zinc would corrode 10 to 100 times slower than other ferrous metals. Selecting the right zinc plating process is important to minimize damage risks on the end product.
Barrel Plating and Rack Plating
In rack plating process of applying zinc coating, the components would be affixed to the jig for holding the parts in place and avoid any potential damage. On the other hand, barrel plating includes placing the components within a custom designed vessel that contains the plating bath. The barrel is slowly rotated during the process in order to apply zinc coats on the components.
Rack plating is usually the ideal process for small, fragile components, which cannot resist the fall downs which the barrel rotation causes. On the other hand, barrel plating is usually more affordable to rack zinc plating and incurs less manual labor. It is considered as the ideal process to plate many components in one go using the bath, which contains a metallic solution in which to-be-plated parts get immersed.
Post Plate Chromate Treatment
This is another means to improve the corrosion resistant properties of zinc plating, making use of a salt containing both chromium and oxygen. Zinc plated parts are immersed in a dichromate solution in the process of post-plating for making the components less prone to oxidation. Post plate chromate treatment would provide an extra corrosion resistant barrier to the component that withstands moisture.
Besides, engineers also apply sealers following chromate treatment. These post-treatment sealers can be applied on yellow zinc coatings, black zinc coatings, black oxide, or clear zinc coatings. Sealers harden the chromate film on the component while enhancing adhesion to zinc coatings. When used alongside chromate treatment, sealers can enhance corrosion resistance of the metal part.