Pressure die casting is ideal for producing high volume components. The parts, commonly known as castings, can be made with thin wall thickness and without having to compromise the quality. The metallurgical process makes use of distinct machines that may range amid 80 ton as well as 1100 ton. The choice of a machine is decided according to the pressure required to cast parts, and the die casting technique involved.
The important aspects to consider when choosing a machine comprise the following. Ultimately, it should be able to assist in producing parts with maximum efficiency and productivity. Thus, each section of a machine has to be evaluated at the time of buying, keeping in mind the performance criteria stipulated by clients.
The Ton Capacity
As said, machines used for metal casting come in distinct capacities that may range from eighty, one hundred and twenty to two hundred and fifty tons or more. The choice depends on the task it should or is supposed to perform.
The Machine’s Base
Since a machine’s structure rests on its base, this section should be strong enough to support the contraption. The base should support its injection system. Foundries also make use of vibration isolators to provide stability to a metal casting machine.
The Die Locking System
Most machines make use of hydraulic systems. The mechanism that supports die locking must be adjustable with abilities to hold all kinds of dies.
The Heat Exchanger Systems
Machines, in general, are subject to failure due to excess heat. Mainly to avoid overheating of the mold, heat exchanger systems are used.
Injection System and Ejection System
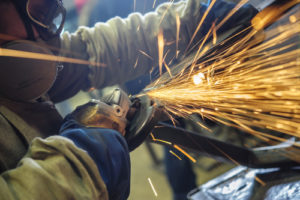
Die Casting Machine
The molten metal injection system operates by relying on a hydraulic mechanism. They are designed to be powered by high-pressure accumulators. On the other hand, ejection systems are used for exactly what the name implies – to eject a die cast component from the die cavity.
The Hydraulic System
It consists of relief valve, double vane pump, accumulator, and unloading valve. The system is responsible for movements of different components, which may vary according to a machine’s design.
The Electrical Systems
The electrical parts of a hydraulic machine may consist of motors, switchgears, relays, contractors, and so forth. They are generally housed in a metal cabinet and are essential to the functioning of a machine.
These are the main things foundries consider while choosing a die cast machine. Apparently, due consideration in the selection and installation process is vital for the quality of work done.