Among other things, the design of runner systems and the choice of alloys play key roles in die casting. It is a metallurgical process, in which molten metal is poured or filled into a die cavity or mold under pressure and then turned into a solidified form by means of cooling. The end output or a die cast component is what the industry terms a “casting”, although generally that is used to refer to the manufacturing process too. The metallurgical process also has a low-pressure type apart from the high-pressure one.
The choice of a die casting chamber, from among hot and hold chamber methods, is decided after considering the type of metal involved in it. The melting point of alloys plays a key role in the choice of the chamber. The melting point differs from one metal to the other. Generally, ferrous metals have higher melting points than non-ferrous counterparts do. Metals with low melting points are easier to die cast since they conform to designs predetermined in the manufacturing process. The main non-ferrous metals used in die casting are zinc, aluminum, copper, and magnesium.
Once the cavity of the die is filled with molten metal, a coolant is circulated around it in order to cool the component being formed in the die casting machine. After that, the halves of the die are separated and the casting is ejected with a mechanism. In high-pressure die casting, it is ejected out of a die mold using ejector pins.
The metallurgical process has evolved much from the yesteryear when furnace heating was the only norm. The safety of the workers and environment are of a prime concern for die casters nowadays. The process also involves the use of robotic technology to make tasks convenient, yet safety is equally important in die casting plants. At the start of the manufacturing process’s sequence, the operators spray lubricant onto the cavities of the die, the plunger as well as the guide bars of the die. As a result of die’s elevated temperature, some of the lubricant evaporates into a plume of fumes and mists. Some key advantages of filtering fumes, mist and smoke generated in the manufacturing process comprise the following:
- Protects the health of the workforce
- Reduces exhaust air make up necessities by up to eighty percent through re-circulated conditioned air
- Extends the die casting machine’s life
- Reduces operational cost through lubrications’ reclamation
- Improves the quality of part and product
- Complies with local, state and federal environmental standards
The contaminants from die-casting processes generally fall into the following two categories:
Metal Oxides – As molten metal is filled into the cavities of the die, and when they are opened as well as closed, an amount of metal will escape in oxide form. It will differ based on the metal and the cavity’s temperature.
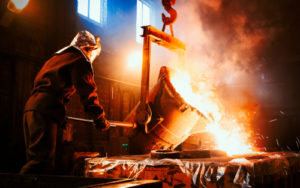
Die Casting Tips
Die Lubricants – The majority of emissions in die casting come from lubricating the main mechanical plunger, cavities and guide bars of the die. This leads to smoke with submicron particles. Breathing this submicronic smoke is harmful to the die casting machine operators. The temperatures of the molten metal can exceed thousand Fahrenheit. Thus, foundries have to use something more advanced than standard lubricating oils as well as greases. Instead, die casters commonly use a mixture of carrier oil or water and graphite as a coolant.
During each operation cycle in die casting, this lubricant’s plume is driven off owing to the high temperatures. It consists of a mixture of light as well as heavy oils, carbon, graphite, and other materials. The consequential contaminant is usually a semi-conductive and grease-like substance.
Die casters adhere to the following two approaches, recommended for fume and mist control.
Source Capture – This approach must be the main one to capture harmful emissions in die casting. It comprises the use of extraction arms or fixed capture hoods situated proximate to the cavities of the die. Capture hoods have to be situated as near as possible to extract airborne contaminants at or close to their source to the machine operator’s safety and to avoid fume from getting into other parts of the facility. This is the most effective way to capture emissions, one that necessitates the least energy as well as initial investment from the die casters.
Ambient Air Collection – When used in combination with the aforementioned method to control fume and miss emitting from a die casting machine, this one can help get rid of the ambient haze caused by pollutants in the air. However, this approach is not as effective for fume and mist control and it does not protect the machine operators or their breathing zone. Thus, it is recommended to follow this method only when it is used in combination with source capture.