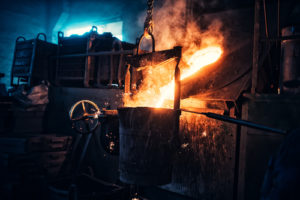
Die Casting Process
Sand mold casting or sand die casting is one of the most popular techniques implemented by several die casting companies to produce non-ferrous alloy casts. It might come as a surprise to many when they hear the fact that the process of sand mold casting was invented approximately 6,000 years ago.
It is true that the process of sand die casting has undergone a number of modernizations and changes over the years. However, the basic principle of this die casting process remains the same. Major commercial foundries, die casters, and even small-scale operators incorporate the use of sand die casting due to the number of benefits it offers.
Experts from professional die casting companies state that the sand that used for this die casting process often varies as per the requirements of customers. Some of the most commonly used types of sand for sand mold casting process are as follows.
Green Sand
In simple words, green sand can be defined as the sand molds, which are formed from wet sand. In some cases, green sand may be referred to as clay. The sand mold will be usually in an uncured state when the metal is poured into it. Sand mold die casting process that uses green sand is relatively inexpensive and quick. However, the downfall of this die casting process is that there is a chance for the sand mold to shift or collapse during the casting.
Water Glass or Sodium Silicate
Sodium silicate is another type of sand, which is used to produce mold casting through the process of sand die casting. One of the highlighting factors of sodium silicate is that it is capable of transforming from liquid state to solid state at a rapid pace when carbon dioxide is passed through it. This in turn hydrates sodium silicate and makes the process of sand die casting extremely simple.
Resin Sand
Resin sand has the ability to become a solid mold with a smooth surface when it is thoroughly mixed and heated. Die casting companies love to work with solid mold because it allows them to considerably reduce the number of defective castings. However, the downfall is that this sand die casting process comes at a higher price and it has a relatively slower production rate.