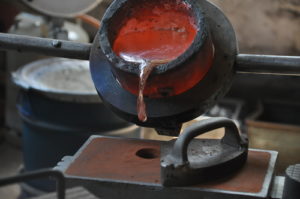
Pattern Allowance Types
Die casters pour molten metal into a mold cavity with high-pressure in metal casting. The liquid metal cools down and turns into a solidified state inside the cavity. Metal casting can manufacture everything from engine parts to building structures or even art pieces.
The mold cavity determines the shape of the casting, but a pattern is also needed to shape it. A mold pattern enables pouring the molten metal into the cavity in high-pressure die casting. The metal then solidifies in the desired shape or the actual pattern employed in the manufacturing process.
There is more to patternmaking than just creating a ditto replica of the desired shape of the casting. The patternmaker of the mold cavity built certain allowances into the mold cavity pattern since they are accountable for the final shape of the component and its characteristics.
Besides shaping the cavity, the patternmakers understand that it should give a casting with right dimensions, that pattern’s shape should pave way to exit the mold cavity without having to cause breakage. It should also compensate distortion and solidification shrinkage in casting and should comprise of a passage that includes gates and runners in order to pour molten metal into the cavity.
Any flaw in the designing of the feeding system may cause a flaw in the end product. However, getting all of the aforementioned necessitates precision from the part of the patternmaker and involves some amount of calculations too. Each pattern of the mold cavity is designed taking into account all of those aspects.
Pattern Allowances in Metal Casting
The draft enables removal of the pattern from each of the mold it shapes in casting process without distorting its dimensional accuracy or breaking it. The right angle of the draft is arrived at as per the pattern’s complexity, the type of the mold, and its surface type.
Shrinkage Allowance
Molten metal shrinks when it cools down just as most materials used in high-pressure casting do. This allowance considers the solid shrinkage in the solidification process or the cooling of the casting, and it compensates the volume with which a metal would shrink. Shrinkage is the lessening of the liquid metal volume.
On the other hand, distortion allowance refers to distort the pattern of the mold cavity purposefully in order to compensate the anticipated cooling distortion in die-cast solidification.