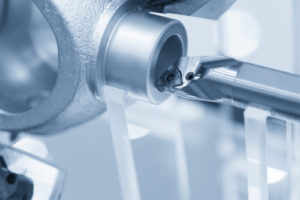
Soundness of Metal Castings
Foundries perform metal casting diligently with a series of steps, which includes designing the casting tools and placement of parting lines with simulation software. Still, for conformance to specifications, foundries test and inspect the casting after they are manufactured. The generic term, ‘specifications,’ might mean everything from dimensional accuracy to mechanical properties and surface finish of the end product.
Most of the time, the criteria for testing a casting is communicated by the foundry as per the request of clients and an efficient method can be arrived at as per a discussion. This is something that adds to the cost of manufacturing, so the terms for testing are discussed prior to requesting a quote from the foundry for metal products. Obviously, it varies according to the application of a metal tool or any other product.
In general, testing of casting is categorized into two, and they are as follows.
Destructive Testing of Metal Castings
This necessitates a separate casting to be manufactured apart from the required number of components by the clients. The casting sample can be subject to demolition, which is done for determining its internal accuracies such as the extent of shrinkage, gas, or inclusions. This type of testing tells the sample’s condition only, so it will not guarantee the internal soundness of other parts. Still, it is a widely practiced testing method by foundries, which are into metal casting.
If the sample part or casting meets the specifications, manufacturing can be continued under an assumption that future parts shall be cast with the same set of accuracies.
Non-Destructive Testing of Castings
Such testing methods, which do not require destruction of sample castings, are used on the cast part for verifying external and internal soundness. The methods used in this type of metal casting testing comprise visual and dimensional inspections, liquid dye penetrant and magnetic particle inspections, radiographic inspection, and ultrasonic testing.
Once the non-destructive testing is finished, the accepted castings can be used as it is, and thereby shipped to the clients. Yet again, more often than not the components can be subject to more processing, including specialized painting, heat treatment, and other kinds of surface treatment methods like hot-dip galvanizing, and even machining, in some cases. The use of further processing of the casting will depend on the test results.