When it comes to product design, the aesthetical compound is what immediately comes to mind. However, this only makes for the outside of what is a more intricate design process. Appearances are essentially bound to the production system, which dictate rules to which a designer should stick. Changes in design occur over time based on the need to conform, but this is further restricted by the choice of material and its productive technology’s state.
Because the aesthetic taste and objects’ functionality are related to the limits of productive systems, the method of processing proves vital.
By selecting die casting as the method of processing, it becomes necessary to consider some essentials, such as draft angles, parting lines, and critical points. The metallurgical process offers an array of advantages, such as a piece’s ease of replication. At the same time, problems in the cooling stage may lead to a decrease of some mechanical traits, such as resistance, which make it essential to intervene and modify the distribution of material, or apply strategic ribs.
The process of component design for casting is linked inextricably to the productive process, which means a constant connection between the client and supplier is required. The purpose of Design for Manufacturability is to create that kind of connection.
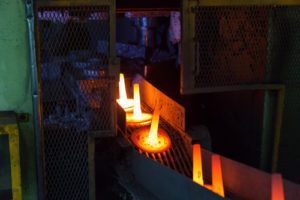
Casting Design
Design for manufacturability serves as a communication bridge between the client, designers and technicians of the supplier. The objective of DFM is to present a product and the correlation of it with production, as well as its replicability over time. DFM is an analysis of technical viability, which means the technical unit should evaluate whether a product design complies with the factory’s available technologies, and the possibility of a cost-effective deal.
After DFM, some changes can be recommended concerning the productive stage or enhanced product resistance, provided they do not impact the required product’s aesthetics or functionality. The requests are comprised in the DFM document, which is typically made up of the following topics.
- Critical areas: the section wherein problematic points are underlined. They may necessitate distinct treatments or structural changes.
- The Deformation Area: Owing to the use of a casting process, it is essential to consider the forces exerted during the demolding phase
- Any discrepancies in plans as well as other clarifications
- Tolerance
- Planning of the position of casting extractors
The document is then repeatedly sent out to qualified offices to find an agreement that matches technical and functional/aesthetic requirements.