Several casting methods are used in the field of metalwork to turn molten metal to solidified shape for use in industrial and commercial applications. Within each metal casting process a cavity is made, wherein the molten metal is poured either with high-pressure or with gravity. After a while, it solidifies and the casting is later ejected from the die or mold.
Metal casting is used most often to produce intricate products, that would other be very complex and pricier to make with distinct methods. Die cast mold making is one of the best methods in this regard. Besides, a metal object is made with several other methods and they are.
Vacuum Casting
Vacuum casting is sand casting’s alternate form, which involves unbonded sand’s use. The process is used often in the manufacturing of nonferrous and ferrous metal molds.
It makes it likely to form molds sans pressurized compaction methods’ use, like blowing and squeezing. Instead of those methods, clean molds are produced with vacuum pressure and dry sand. Vacuum casting lets manufacturers do away with sand mixer and other types of equipment necessitated for hardened sand.
The process can also be carried out using a collection of tools that consist of a vacuum system, a flask, a pattern, a film heater, and vibration surface. It is usually clean and devoid of odors or fumes. Once completed, the dry sand is recycled for the subsequent application. As such, it is one of the waste-free processes by which molds for metal products are cast.
In the casting process, patterns are positioned onto boards that have vacuum chamber vents. Then, heat-softened plastic or sheets are placed over pattern and vacuums are activated. This leads the plastic material to wrap firmly to the pattern’s details. Once the pattern is solidified, it is detached from the mold. After that, a vacuum process is used to pull the molten aluminum through cavities.
Vacuum casting is often preferred since it can produce finishes with accurate dimensions. A number of shapes can be produced with it, whether the mold is heavy or lightweight. It lets manufacturers reuse patterns many times over and leaves little excess scrap material on completion.
Graphite Permanent Mold
This process involves steps similar to permanent aluminum mold casting but uses graphite molds. To start, the metal in a molten state is poured into what is described as a gating system in order to fill the cavity formed by graphite mold. Once it solidifies, the surrounding molds in graphite form are separated and castings are removed. In certain cases, the molds are also cooled with water channeled through the mold.
Often, graphite molding is preferred in industrial applications since it gives a fine finish for metals’ surfaces. Such types of castings are good at forming accurate details on molds. As such, an array of machine components can be produced with graphite casting.
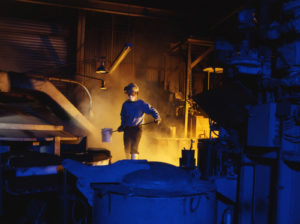
Requirements For Casting Process
Examples of products that might have graphite cast molds could also comprise several parts of monitors and speakers. Knobs and latches on doors and drains and faucets on sinks are sometimes made with graphite casts.
Often, everyday tools are also the result of graphite die casting. Screwdrivers and wrenches are often made of graphite castings, as are several fasteners holding pieces together below furniture. Other products usually made of them comprise pistons, pipe-fittings, gear housings, and splines.
Steel Die Permanent Mold
It consists of a method similar to graphite casting but is usually geared toward relatively heavier loads. While in contrast graphite is suited mainly to aluminum alloy, this particular method can be used to cast molten aluminum, iron, bronze, and lead. It is often used to manufacture metal automobile accessories, machine parts, and spare parts.
The steps comprised with it can be split into several steps and they are mold preparation, filling the cavity, releasing the mold, and trimming the excess material. The initial step is to coat mold halves using refractory material, and bring them together in order to form the cavity wherein the molten metal will solidify, once poured into. After that, either gas pressure or gravity is used to fill the cavity entirely.
Some time should pass to let the molten metal harden and take the desired shape. Once it has solidified, the cast’s two halves are opened and the casting is freed. At this point, excess component material is trimmed off it and finished output is buffed if desired to a finer finish.
Plaster Mold Casting
This is the process wherein molds are formed using enhanced Plaster of Paris. A plaster mold is disposed of once an object shape has been formed. For additional strength, it is mixed with magnesium oxide or talc. Unlike sand, though, plaster mold can be only used to shape nonferrous metals.
They are often employed in the manufacturing of lock parts and several machine components, comprising fittings, gears and valves.