The business of casting aluminum or other components for the automobile segment become competitive when the industry is going through troubled times or facing trade issues. In such times, the tolerance for high scrap rates or downtime is much less. More often than not, porosity in a die-cast component become a source of manufacturing headaches for foundries.
First, it has to be noted that each tool used for casting aluminum or parts made of other materials requires air evacuation. Nowadays, with developments that have taken place, a strong case for using the vacuum technology over conventional vent system can be made to help lessen the porosity and other metal casting issues. Currently, there are two approaches to the use of vacuum technology, and the advantages derived from both are as follows.
On assessing these advantages, more and more die casting companies are moving from conventional venting to the right use of vacuum technology. That is because it is an assistive approach, which eventually helps die casters to manufacture better quality components.
The Vacuum Technology
They will often say that the option between conventional venting as well as vacuum is based upon the component requirement and preference of customers. However, making cost comparison prior to deciding on one might leave them pleasantly surprised. Consider the advantages of vacuum as mentioned below.
Conventional venting is relatively less effective to vacuum since there is not sufficient overall vent space for the cavity to efficiently evacuate. In the venting process, the press does all the work, while a vacuum system assists it in evacuating the cavity. It is more efficient and there are less machine and tool wear and tear, saving manufacturers maintenance time and cost, not to mention component fallout.
Vacuum systems’ use decrease gas porosity in a component or casting. This is one of the main benefits since porosity can be alleviated with the vacuum assistance, although it cannot be fully eliminated.
Three distinct kinds of porosity occur during die casting. One of them is merely air in metal feed sections and the die cavity. The gas created when hot metal that is being fed hits lubricant is the second kind of porosity. The vacuum technology helps to alleviate both. The third type is shrinkage. The process control is actually a more significant factor in reducing it, and the said technology has little to do with it.
Many of the companies who are into die casting say that vacuum vents help produce better quality components since they help decrease poor fill and porosity-induced scrap rates.
Other advantages of the technology comprise better surface finish and mechanical properties of metal components being cast. It decreases out-gassing, thus improving the painting as well as plating quality. In addition, the higher the casting’s density, the better will be the weldability and leakage factors.
The porosity’s location is also critical. In case the air is close to the surface when components heat up, it will expand and could lead to blisters or holes on their surface during plating or powder coating. Vacuum blocks’ use means scrap will be less since die casters can reduce the porosity in the component, and can prevent other issues that can come downstream during the machining process.
In today’s competitive market, where metal casting business is taking on more and more intricacy, it is tough to overlook the benefits of vacuum technology’s implementation to increase the uptime and reduce costs.
Valve vs. Valve-less Vacuum Block Systems
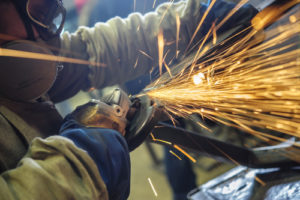
Advantages Of Die Casting
While valve style blocks necessitate moving parts, valve-less ones have none of them. In the former, a valve with a particular design is necessitated to shut off molten metal’s flow during shot cycle and keep it from plugging vacuum system. Moving parts subject to wear are there and necessitate routine maintenance before, during and/or after the use of the system. When it will be necessitated is not completely predictable, though, and component parts have to be inventoried in order to make sure the system’s continued operation.
The other type of vacuum system makes use of no moving parts as said in the path of the metal flow. Instead, it utilizes resistance to the metal flow and solidification of molten metal in order to shut off the vacuum and flow. Besides, blocks are heat-treated with H13 material, and cooling lines can also be included in them to assist in the metal solidification.
Valve style systems make use of both the flow of metal through a secondary vale or even electrical switches and a cylinder in order to shut it off using the valve; while valve-less systems pull the vacuum during the entire shot cycle until the metal hardens.
Due to their intricacy, experience has revealed downtime is associated with these systems to a great deal, further adding to the vacuum’s total cost and avoiding several die casting companies from implementing vacuum assistance as a means to enhance the quality of casting. The valve-less vacuum technology’s simplicity is changing that way of thinking. Besides, the moving parts in a valve-style block have to be both maintained and swapped on a regular basis; while, valve-less style blocks necessitate no maintenance.
Several moving components can make the former system expensive to implement and maintain. Whether timers, limit switches, and/or programmable logic controller is used in order to control vacuum valve’s open/close mechanisms, they are costly to both install and maintain and also subject to failures. The more complex the system, the more likely it will not perform, in a die casting setting.
Take, for instance, fillers being used on most of the systems. They are necessitated to avoid the gases’ flow, residue and the metal from damaging vacuum pump, secondary vales as well as gauges. In case maintenance is not done on a routine basis, in many cases filters plug up, decreasing vacuum system’s effectiveness. A filter that is free flowing and does not necessitate the level of maintenance in the conventional process is available.
In the latter system, valve-less blocks are being designated by the size, relating to the space available to pull required evacuation. Operators have to determine vacuum area necessitated before ordering a particular model of block. Calculations to determine its size are given by the supplier or software that can facilitate the same. Usually, the formula to determine the required vacuum space computes the metal feed system’s overall volume, comprising part as well as fill time. Besides, there are safety factors built into this formula to make sure space is sufficient to achieve the cavity’s evacuation.
Valve-less blocks can be utilized in casting aluminum, zinc, and magnesium parts. Several of them have lasted over 100,000 shots sans repair. Full systems comprising tank, controls, pump, gauges, and filter are available, as is the design assistance.