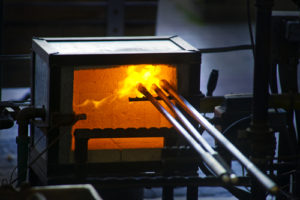
Secondary Alloy Choice
ZAMAK molding is done to create components with zinc alloys. ZAMAK is an acronym that refers to a family of alloys used in zinc die casting, with zinc being the base metal, and aluminum, magnesium, and copper being the secondary mating materials. It proved to be ideal method to manufacture zinc die-cast parts in foundries that it has become synonymous worldwide with zinc die casting.
ZAMAK alloys have noteworthy mechanical properties, the most notable of which is higher rigidity to standard aluminum. Furthermore, it is significant to note the less popular physical properties of ZAMAK alloys to determine if it can be used in molding applications. Such properties of the material include electromagnetic shielding tolerance, higher vibration damping rate, non-sparking, and corrosion resistance.
Some of these properties enable the Mexican die casters to make components such as heat sinks with desired physical characteristics in ZAMAK molding. Alloys with less than four percent aluminum, eight to twenty seven percentage aluminum, and patent alloys are some popular zinc alloys used in ZAMAK molding. The alloys that are ideal for die casting with hot chamber include Kirksite Alloy, Zinc Alloy 3, Zinc Alloy 5, and Zinc Alloy 8. Such types of ZAMAK alloys have 2.5 to 8.8 percent aluminum.
Aluminum is mated with these alloys due to three reasons. Firstly, aluminum helps lessen the alloy’s melting point, and thereby, reduces the required thermal energy of the chamber and provides energy cost savings. It also lessens the corrosion level of the ZAMAK alloy toward steel. Since the melting point and the die comprise of steel in ZAMAK molding, the reduced corrosion level would yield better durability of the tool.
Aluminum also betters the alloy’s fluidity and makes it plausible to get thin wall depth and ease the molding process. If an alloy does not have aluminum’s properties, the fluidity of the alloy reduces and the probability of solidification cracking and sticking tends to increase in the solidification phase of ZAMAK molding.
Further, copper is another secondary component in terms of percentage quantity in ZAMAK alloys. That can range from zero to up to 3.5 percent. Mating copper is up to the discretion of the die caster. Even though its presence may improve the component’s mechanical properties like wear and tear resistance and hardness, copper may also lessen the percent elongation at melting point and the tenacity of the alloy.