In several mold and die shops, the choice amid the ram EDM process and CNC milling process is far less obvious than ever before. The changing technology is also changing the rules.
Milling can be applied even more broadly today. Machining centers that are capable of following intricate and precise tool paths at top feed rates made it cost-effective to use fast and lighting milling as a substitute for EDM in several applications that involve hard metal, complex detail, and smooth finishes.
The EDM technology also has gotten better, though. Die/mold operations managers often advise people as to which of these metal removal processes make sense for their task. There are no clear-cut answers, but there general rules that govern decision making. The following comparison between EDM and high-performance milling summarizes those general rules. There are not the only considerations, though, to decide on one.
When to Use Electrical Discharge Machining
- For sharp internal corners: EDM will remain the better process for inside corners until the square end mill becomes perfected.
- For most intricate geometry: Particularly, it makes sense when the intricate surface is difficult to reach for a (milling) cutter.
- For deep cutting: More specifically, steer clear of milling where tool’s length to diameter is especially high.
- For unattended cutting: EDM is the easier method to automate, as it is predictable than the milling process. In a process using robots to load electrodes and workpieces, an EDM process that includes electrode production can effectively run around the clock with minimal operator intervention.
- For high-expertise components: Generally, programming time is even shorter to mill an electrode than it is to mill the form in metal. In more sophisticated processes, the difference is even more pronounced. The required programming time to allow a machining center to do work once considered EDM-only is perhaps sufficiently high that it remains the expedient option.
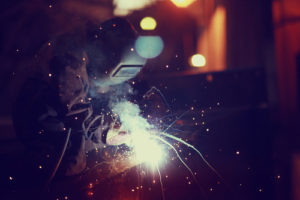
Interesting Die casting Facts
If EDM finish has been specified, the quality of surface it can deliver would be much better. Additive-related advances, for instance, not just improve the finish graphite electrode can get, but also lead to a shallower heat-affected zone (HAZ).
When to Use the Milling Process
- Use it whenever you can, says experienced die/mold operations managers.
- For a non-cosmetic surface, as well as for a surface to be textured. EDM adds one more step in texturing. Unlike milled surfaces, one that is “EDM-ed” generally necessitates polishing before texturing.
- When the access is easy. When the geometry is open as well as the above-mentioned ratio is low, it is best to mill away excess material from a surface.
- For family components. Groups of comparable workpieces as well as multiple-cavity tools present the chance to amortize the time spent upon programming, comprising the time spent upon learning the ideal way for milling the form.
- For components that cannot have a heat-affected zone.
- Where high precision is necessitated.
- When the EDM operators are scarce. In several shops, usually personal considerations take precedent over technology-related considerations.