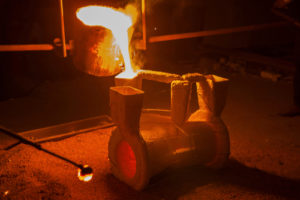
Die Cast Light Fixture
Aluminum die cast components usually weigh one-third fewer than such parts made of steel, whilst providing durability and strength required for lighting fixtures for both indoor and outdoor usage. Being a malleable material, aluminum is preferred by foundries to manufacture light fixtures since it can be molded into thin wall components with intricate geometrical shapes.
The capability to customize the material enables foundries to meet a part of the requirements of lighting fixture suppliers as per the demands of consumers. A major benefit of choosing aluminum to die cast light fixtures for lighting industry is that is a cost-effective material. It is done by pouring molten metal into a die cavity and turning it into a solidified shape by cooling the die. Compared to light fixtures produced through alternate manufacturing processes, die casting is very cost-effective and straightforward process.
One such procedure is extrusion molding, where cold or hot semi-solid materials are pushed through an extrusion die or an opening that helps form a shape resembling a tube or pipe. Does that mean extruded light poles made of aluminum are stronger than die cast light poles made of the same material? It can be thicker, but stronger may be an afterthought.
There is a misconception among non-professionals that as certain metal extruded poles have a thicker wall, when compared to die cast aluminum poles, it translates to better durability or wear and tear resistance. However, that is not necessarily so. Extrusion is used to produce components in large quantities and reduce manufacturing costs through fast and convenient fabrication. The geometrical shapes produced by extrusion molding should conform to uniformity and cannot have complexity.
To put it in layman terms, one can compare extrusion to the process of injecting semisolid modeling compounds via a pasta rolling machine. The manufacturing process puts stress on a material and lowers a component’s quality. So it must be thicker to withstand that pressure.
Die cast light fixtures are formed by pouring molten aluminum into the die opening. The components can be intricate in terms of shape and geometry. In aluminum die casting, the metal will not be put to extreme stress and is allowed to cool to a temperature level that will not weaken the metal’s integrity. Castings are thin in most situations, but that is because the metallurgical process does not require thicker aluminum to compensate for the lost integrity and strength from extrusion.