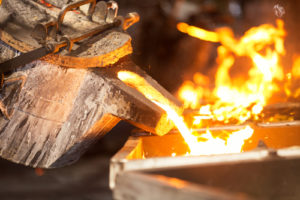
Metal Casting Processes
Two most significant processes in metal casting are adjusting the temperature to suit the melting point of metals and pouring the motel metal into a mold. The melting point refers to the temperature required to melt a solid metal; it is one, which varies from one metal to the other. For instance, the melting point of brass is not the same as aluminum. In metal casting, the temperature depends on the type of metal and the density required for a casting, which is made by pouring the molten metal in a way it solidifies itself and conforms to a predetermined shape.
Aluminum’s melting point is 660 Degree Celsius. However, if the metal used in the casting process has a higher melting point than that, foundries use certain mechanisms to control the temperature. If a furnace is used in metal casting, often a pyrometer and the temperature controls in a melting furnace are used for that. It is important to keep the temperature levels as constant while pouring the motel metal into the mould, to make sure it conforms to the required quality standards or specifications of the end product.
In case the molten metal is excessively hot while pouring it, it will change the casting’s physical and chemical properties. If it is too low, on the other hand, the motel metal’s flow into the die cavity or its fluidity to some of the internal cavities of a casting may get affected. So, the foundry workers monitor this temperature to ensure the integrity of the component.
A casting’s density is another important aspect to consider in metal casting’s early stages. To achieve a thin casting, it is important to pour the molten metal quickly as opposed to a much thicker casting than that. The logic for that is pretty much the same: to avoid molten metal from getting cooled down in a way that it affects fluidity.
On the contrary, if the metal is being poured quickly than the required speed, it may introduce a turbulent flow in down sprue or some of the other parting systems that fill the molten metal into the mold. This may cause some unwanted defects in the casting. To avoid that, foundry workers must have expertise in judging the accurate temperature and right pouring rate needed for each casting.