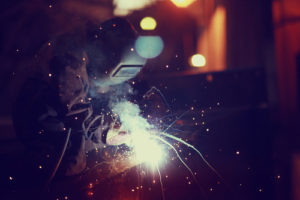
Zinc Die Casting
Chrome plating on zinc casting are used on exterior parts of automotives. Everything from door handles, side panels, and window trims, to emblems and logos made of zinc are chrome plated for an added styling.
Aside from automotive, foundries use chrome plating on zinc castings for making an array of mechanical components. Zinc can be casted at mild temperatures, and hence, they provide energy savings to foundries compared to other mating metals and alloys. Nickel chrome plating is a traditional method to enhance the surface properties of zinc castings. In fact, it traces back to the chrome plating on vintage cars of the mid 1900’s.
The starting step of plating chrome on the zinc die casting is cleaning of the base material. This may comprise of cleaning the casting to clear any impurities on the surface or removal of grease from the casting. This is an important step of any chrome plating procedure and is done to make sure an even surface finish on the component.
Besides, pre-process treatment of the surface is significant too when laying chrome plating on zinc casting, since alkaline and acidic solutions are subject to dissolve the material if not pretreated appropriately. To prevent that, foundry engineers thinly coat cyanide copper flash on the zinc casting, which is done to protect zinc from acidity in the subsequent procedures. The non-acid copper flash will adhere to both chrome plating and zinc casting, and will ensure compatibility of both mating materials.
The next step in plating zinc casting involves layering acid copper on the component surface. Foundries use copper for increasing the electrical conductivity of zinc and to make the surface look even more uniform. Nickel layers are also used to give the component a barrier that will resist corrosion in future. Chromium is applied after that on zinc die casting for giving the component surface a sheen look, and for protecting nickel against not only corrosion but also wear and tear.
Apart from that, initial polishing or buffing the surface also necessitates for obtaining a desired finish on the casting, especially for automotive, hardware, or electrical applications. Following that, zinc casting’s surface gets electroplated using a heavy layer of copper in the process known as copper plating. The components get rebuffed for making the copper surface smooth, followed by activating the copper plating and electroplating using chromium and nickel.