The metal shaping process of die casting allows us to produce metals with desired shapes and superior properties with ease. However, in some cases, the finished product may contain a few defects and other issues. These kinds of defects may happen if you fail to control the die casting temperature. This is the major reason why businesses seek the help of professional die casting companies when they want to produce a finished product from a die.
The yield and tensile strength of die casting alloys will considerably decrease as the temperature of die casting increases. So, aluminum die casters put in extra efforts to ensure that the temperature of the process is controlled. If you are looking to produce parts with greater tensile strength, then you will surely need to control the temperature of the process. If you fail to do so, then the strength and hardness of the finished product will be compromised.
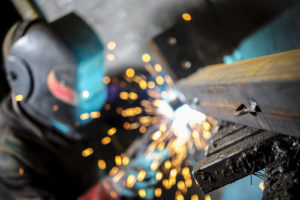
Metal Die Casting
Another important thing you need to note is that the ductility of the die will also increase as temperature increases. However, the changes will depend on the type of die or alloy that is being cast. For example, aluminum alloys are relatively less ductile when compared to zinc alloys. So, die casting companies will have to observe the properties of alloys and learn about the changes in order to maintain a controlled temperature for the process of die casting.
Aluminum is one of the most common choices of die casters when it comes to metal die casting. Aluminum alloys are highly durable, lightweight, and has excellent corrosion resistance. The tensile and yield strength of Aluminum 380 alloy are 45 and 24 KSI (Kips per Square Inch) when the temperature is around 200 degrees. The yield strength of Aluminum 390 alloy ranges from 18 to 41 KSI at 500 degrees.
Zinc is another popular alloy that is used for the process of metal die casting. The excellent properties of zinc alloys such as ZAMAK 7, 5, and 3 has enabled die casting to produce excellent metal parts with desired shapes. The yield strength of most zinc alloys is 40 KSI at 75 degrees. However, the yield strength gets reduced to 10 KSI when the temperature is raised to 275 degrees. This implies that the yield strength of zinc alloys decreases as the temperature increases.