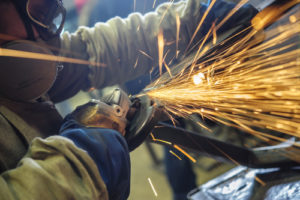
Advantages Of Metal Casting
In full-mold casting, foundry engineers use thermally decomposable materials such as polystyrene foam to cast patterns. This metal casting process, which is akin to lost-wax casting, evaporates the foam by pouring the molten metal directly into the mold. Thus, the casting process is expendable. The polystyrene patterns in full-mold casting can be designed using a computer-aided software, which helps to make changes to its design prior to the actual casting process is completed. It is explained in detail below.
How Full-Mold Casting Works
The patterns are made with materials that disappear during the metal casting process. Once it is coated using a refractory material, the patterns are used in single piece sand molds. The benefit of this process is that molds with intricate designs can be cast without having to use a draft for that.
The patterns in small quantities can be handmade or produced in a machine using a solid foam block in full-mold casting. As part of small quantity runs, the patterns can be cut using hand tools or automatic machines using a block of foam that is solid. For big volumes though, the material for the pattern can be inserted into an aluminum mold that is preheated and then steam is exerted to the material. After the pattern is ejected from the aluminum die, spruces and gating systems can be glued or hot glued to be precise into the polystyrene pattern.
Then, the pattern is placed into a molding box prior to ramming it for hardening the sand, and the gating systems and spruces are applied to the mold to allow molten metal enter each design and cutting made by it. Then, molten metal is poured on a pattern that is made up of polystyrene material, and once the metal in a liquid state comes in contact with the pattern, it disappears or evaporates and forms the mold cavity’s shape.
The Applications and Benefits of Full-Mold Casting in a Nutshell
Many products made of iron, nickel, and copper alloys, steel, and aluminum can be cast using this metal casting method. The castings with complex patterns such as manifolds, auto-brake parts, and pump housings are cast too.
Full-mold casting is beneficial to complex castings that are typically made with the use of drafts and cores. It is an effective process for small scale and large-scale mold manufacturing, and saves production time, as the polystyrene pattern does not require to be shaped such as in wood patterns.