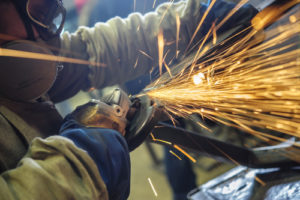
Modify Surface Finishing
The term “processing technique” is a generic one used by metal finishing engineers in reference to the processes in the last phase of component manufacturing. Most of the processing techniques leave a unique texture on a metal product’s surface, especially zinc castings, thereby giving an overall pleasing appearance even without coatings.
Some of the processing techniques for modifying a casting or a manufactured product and the effects it leaves on the metal surface are listed as follows. Note that these techniques are used by die casters to improve the surface of zinc castings in particular.
Abrasive Blasting
It is the process of exerting a stream of abrasive material against a metal’s surface. Abrasive blasting can be used not only for making a metal less rough but also for removing the contaminants on its surface. Among its different types, one of the high-pressure abrasive blasting techniques is done with sand. The result of sandblasting is a casting surface akin to one that can be achieved using sandpaper.
Chemical Mechanical Planarization
Abbreviated as CMP, this surface finishing process combines mechanical and chemical forces, is implemented with the use of a rotational tool, and used for evenly applying slurry so that a polished metal surface shall be achieved.
Electropolishing
This process, which is used to give a shiny appearance to a metal using electrolysis, is similar to electroplating except for that it works in reverse. A metal part is immersed in electrolytic bath serving as an anode and having particles that are drifted toward cathodes.
Although its main application is to make a metal’s surface smoother, there are other purposes to the process since it can be used on objects that are unevenly shaped. Usually, metal finishing industry players use electropolishing for passivating and polishing, but it can be used for deburring metal components.
Thermal Deburring
This process makes use of methane gas combustion inside pressurized chambers for removing flashings, burrs, or other contaminants via oxidation. This metal finishing process is efficient, in particular, for shafts and internal holes that are usually tough to reach and deburr using other techniques.
According to the products and the materials used in manufacturing, you can choose from different surface finishing processes. You can get in touch with die casters in your area to know which one is ideal for which metals.