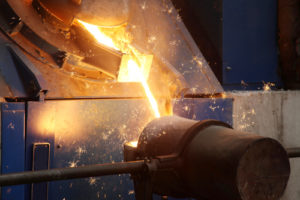
Semisolid Metal Casting Benefits
Combining the die filling process done with semisolid materials, and high-pressure used for feeding solidification shrinkage, allows foundry engineers to produce castings of exceptional quality and extremely low porosity. While standard die-cast parts usually have levels of porosity measurable in full percentages, and porous content in liquid metal forging is usually measurable in tenths of a percent, with semisolid castings, these readings are lower. Such levels of porosity help foundries manufacture castings with exceptional mechanical properties, which can be at or above par in terms of quality, while costing less than is achievable with liquid metal forging or low-pressure permanent mold casting.
Thus, properties influenced by porosity, as well as defects like fatigue and elongation, tend to be better in semisolid metal castings than in competing processes. Besides, due to the absence of residual porosity, semisolid castings can be welded. Another benefit of semisolid casting, as opposed to conventional metal casting processes including squeeze casting, is extended tool life. In metal-mold casting, the number of outputs that can be manufactured prior to the onset of thermal fatigue and subsequent failure of a tool is influenced by 2 aspects:
- The overall heat load applied on a die; and,
- The difference in temperature between an incoming metal and a tool.
These two factors which influence the manufacturability of parts in semisolid metal casting are explained in detail below.
The heat load exerted on a die is a consequence of the tool absorbing heat from aluminum that is solidifying. The extent of heat load can be influenced by 3 factors, namely superheating of liquid metals, the solidifying metal’s latent heat, and the specific heat necessary for cooling a solid casting. That last part derives from the temperature required to eject the casting out of a die.
In liquid metal forging, where liquid metal is being injected into a die at 730 to 735 degrees Celsius, and the solid casting is being ejected about 425 to 430 Degree Celsius, the measure of heat load falls at around 900 joules per gram. On the other hand, the overall heat load from castings produced in traditional die casting is a bit lower, since the output required tends to be thinner. In contrast to both these processes, the heat load in semisolid casting is about 500 joules per gram, since the temperature required to inject semisolid alloys with partially solid content can be as low as 575 Degree Celsius.