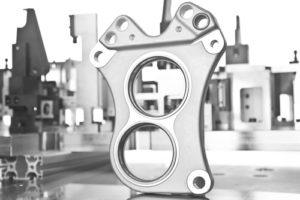
Die Casting Materials
As you would probably know, all solid metals can be cast to produce high-quality finished products with the desired attributes. However, several die casters prefer to work with ferrous metals because of the impressive properties of these metals.
In simple words, ferrous metals can be defined as the metals that contain iron. Most of the ferrous metals available in nature are dense, corrosion resistant, highly durable, and less prone to damages when casted. The same properties are also seen in several alloys of iron, which is why die casters use them for a number of casting process. Some of the most common ferrous metals and alloys that are used in die casting are as follows.
Cast Irons
Cast irons are actually a type of iron alloys whose carbon content is greater than two percent. These dense iron alloys are relatively expensive, but they have a better flowability at low temperatures when compared to steel. This implies that cast iron can easily flow into the complex mold parts of the cast with greater efficiency.
In addition to that, most of the basic cast iron alloys have exceptional compression properties. However, the issue is that these alloys are brittle, which means that they might get fractured or broken if subjected to greater pressure.
Grey Iron
Grey iron is one of the common ferrous alloys used in the die casting processes. The distinct grey color of these iron alloys is due to the presence of graphite inside them. Grey usually contains 1 to 3 percent silicon and 2.5 to 4 percent carbon. The silicon content in these allows plays a crucial role in stabilizing the graphite.
Grey iron is relatively inexpensive but it has a greater flowability than steel in the molten state. The presence of graphite has made these ferrous alloys a lot less brittle than cast irons.
Ductile Iron
Ductile iron is an alloy that contains silicon, carbon, and a few other elements. The percentage of carbon found in ductile iron alloys is estimated to be around 3.2 to 3.6. The best thing about ductile iron is that it has higher ferrite levels, which is the major reason why it is used in cast manufacture.
The spheroid shaped graphite in these iron alloys has increased their corrosion resistance. Ductile iron alloys also have a greater tensile strength and they last for a very long time.