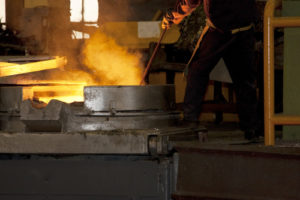
Die Cast Component
Castability refers to the way of manufacturing a high-quality die-cast component with least minimum tooling cost, energy consumption, and by keeping rejections to a bare-minimum. Castability can be achieved if die casting companies maintain a balance between process capabilities and meet product requirements within a time frame that is fixed by the client. Read on to know about the three aspects that tends to affect castability.
Raw Material Selection
The materials used in pressure die casting include non-ferrous metals such as aluminum, zinc, and magnesium. The materials should be chosen as per the required mechanical or physical properties and certain metallurgical aspects, such as melting point, resistance to corrosion, and its tensile strength. The die-cast metals comprise of other properties such as solidification capacity, pouring temperature, fluidity, etc. All of these aspects would affect the end product’s quality, especially in terms of dimensional strength as well as internal reliability.
Geometrical Design
Depending on the intricate geometrical shapes involved or required on a component, its designing will be cost-effective. Designing the required geometry would also depend on tools used in the metal casting process. The design principle, ‘directional solidification’, states that molten metal should form in a casting in a way that the material being fed stays available throughout for the shape that is being turned into a solidified form.
Solidification in long, thin, sections of a die may seem quite tough in the casting process that makes use of a runner system. Henceforth, to return a smooth surface pattern, it can be executed in a planned way in a mold’s drag section. Foundries can arrange high-end equipment to handle finished components, while shipping, machining or assembling the casting. Other than that, a probable breakage in one of its section that is heavy can be prevented with the use of ribs or additional strengths.
End Product Quality
Technically, the end product in die casting process is referred to as casting. The output should be devoid of defects or it should be left to a bare-minimum to meet the castability requirements surface quality, dimensional accuracy, internal reliability, etc. To test the quality of a casting, foundries make use of radiography or pressure testing. Several factors including cold shuts, microporosity, and dimensional inaccuracy may lead to rejections. Note that the last two defects may lead to a turndown only if client specifications are extremely stringent.
Generally, die casting companies employ an efficient product designer, tool maintenance division, and knowledgeable metalworkers in the foundry to complete the casting process successfully.