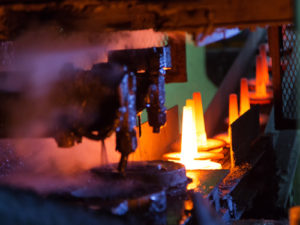
Continuous Casting Processes
Die cast shapes used in strand casting are being produced by pouring the molten metal into a horizontal or a vertical mold cavity and then turned into a solidified state. The rapid cooling of molten metal in a mold cavity used in continuous casting achieves a uniform structure in a solidified metal with desired mechanical properties. Once the cast part solidifies in the mould, it will be cut into a length desired by the foundries.
The common cast shapes being produced in strand casting are solid and tubular, but irregular shapes including hexagonal and rectangular can also be cast in order to match the profile of an end product. Since the continuous die casting functions as a gravity-fed, bottom-flow manufacturing process, it reduces probable trapping of dross and dirt in a casting. The foreign matter in a crucible furnace floats atop the melt; hence, it will not become a part of the casting.
Low temperatures used in continuous casting coupled with a cooling mould cum vertical solidification achieve a grain structure that is uniform in the casting with high density. A horizontal strand casting process is also adopted by foundries to produce cast shapes. Yet, the basic principle of pouring the molten metal and solidifying it remains the same as in vertical continuous casting, except for the equipment extrudes out in a horizontal direction.
Hollow extrusion billets are used to cast a cylindrical-shaped object in horizontal strand casting. It can offer several benefits to foundries and they include the below ones:
- Capability to cast standard-shaped objects and products in irregular dimensions if cast on an elongated tubular form, which is tough to replicate in alternative methods to strand casting.
- Casting is achieved uniformly and densely in terms of structure with consistency and hence is suitable for pressure molding applications.
- If the net-shape of a casting is optimized in continuous casting, the required stock of cast material to finish manufacturing a final component tends to be lesser than that required for castings manufactured with alternative methods to strand casting.
- Castings have an inherent benefit in terms of physical properties of the material over alternative methods, all thanks to cooling and molten metal’s directional feeding in solidification stage.
Products achieved in continuous castings can present cost efficiencies to alternative castings if the cast material, shapes as well as sizes are optimally selected.