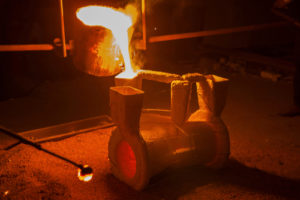
Die Casting Mold Life
The aluminum alloy die casting mold is a crucial aspect of the production process. Due to its frequent use and cost during production, it is necessary to maintain the mold to ensure uniform quality in all its future casting operations. Such maintenance techniques are utilized across the entire die casting process, to produce optimum results in the casted components.
It is important to extend the service life of the die casting mold for maintaining its functionality. This is done via certain processes during the production such as mold cooling, regulating the mold temperature, and maintenance of the signal line. Following these processes can help restore the efficiency of the die cast mold, and extend its lifespan.
Utilizing Mold Cooling System
One of the most effective ways to extend the service life of the die casting mold is by using a mold cooling system. It can help improve the lifespan of the mold, along with enhancing its efficiency of production. Maintaining the adequate temperature is important, as the die steel has only limited tolerance levels to high temperatures. Cracks can form easily on the surface of the mold core if it is used at higher temperatures.
This can also result in the mold core color changing. Other than cracks in the mold surface, it can also result in the release agents getting chilled. Cooling water can help minimize the release agent from getting utilized excessively. It can also extend the service life of the mold, and maintain the quality of the casted products.
Preheating of the Mold
Preheating of the mold is another technique that can increase its lifespan. Usually, cracks can occur when the hot molten metal is poured into the mold, which results in a quick exchange of temperature. Preheating the mold can prevent the formation of any cracks due to such processes.
It is best to heat with a blowtorch or gas if the mold has a complex design. A slow press shot is perfect for a simple mold design, as preheating can actually prepare the mold surface for accepting the high temperatures of the molten metal.
Maintenance of Signal Line
Any contact of the signal line between the die casting machine and mold is to be prevented if the mold has an inbuilt neutron flux measuring. Short-circuiting is common during the production process due to the contact of the signal line with water, and the breakage of the contactor. The mold can get damaged due to faulty signals that cause alarms and automatic stoppage, losing time or chaos signal.