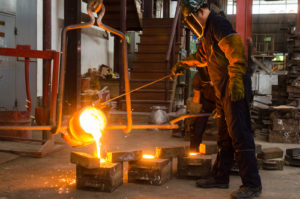
Squeeze Casting Overview
Squeeze casting is a manufacturing process, which combines both die casting and metal forging. It can potentially provide a casted component with highest attainable mechanical properties on the final part. Squeeze casting is acquired by original equipment manufacturers to make aluminum alloy parts, which are yet to be commercialized properly.
The process begins by pouring the molten metal into a preheated die’s bottom half. As and when the metal begins to solidify, the die’s upper half closes and begins to apply pressure. This phase is known as solidification stage of squeeze casting. The pressure applied in the process will be drastically lesser than in metal forging.
The pressure and the molten alloy’s contact with the surface of the die in squeeze casting. It will ensure the end product has mechanical properties that are improvised alongside less porosity. Foundries use coring alongside squeeze casting for forming recesses and holes on the component. The process is used to make parts using both ferrous metals and non-ferrous metals.
Types of Squeeze Casting
Liquid metal forging is done directly in the equipment, which resembles metal forging process. That is because the molten metal is poured into the bottom half of the die, which is contained inside a hydraulic press, whereas the die’s upper half is closed. A high pressure is applied to the entire cavity until the component solidifies. The pressure is usually 100 Mpa or above.
The second type of squeeze casting is indirect, which resembles die casting since the chamber used is similar. The equipment used in indirect squeeze casting can be a horizontal or vertical chamber. The cleaned and grain-refined liquid metal gets poured into the shot sleeve of either types of chamber used in metal casting. The melt is injected into the die via relatively big gates, and at a velocity of less than 0.5 m/second in indirect squeeze casting. The molten metal inside the die cavity is solidified afterwards under a pressure range of 55 to 300 MPa.
The solidification process of squeeze casting will improve the tensile strength of the component improves by several notches in most cases. The process is offered by foundries cost-efficiently, and at the convenience of clients. The manufacturing process often benefits OEMs in automotive segment with a high requirement for chassis frames, steering knuckles, etc., which are made of aluminum. When it comes to marine industry, squeeze casting is used to manufacturer propellers for ships.