Die casting allow the cost-effective making of narrowly tolerated components that have several useful characteristics. Further optimizing mechanical properties by means of both heat and surface treatment is possible in certain cases.
Die cast components produced in the traditional way are deemed to be non-heat-treatable, or with difficulty only. That is because gases are either dissolved or trapped in molten metal. When such components are subjected to higher temperatures necessary for heat treatment processes, the gases expand as well as form bubbles, with a negative impact upon the cast parts’ mechanical strength as well as dimensional accuracy. Procedures like the vacuum and laminar die casting offer a way out.
Precipitation Hardening
Components made of alloys that are heat-treatable and manufactured using the said processes can be heat-treated later. It is characteristic for vacuum die casting that a casting machine’s all areas reached by the melt are evacuated. In addition, the gases that arise when this melt flows in are exhausted continuously by a vacuum.
On the other hand, when using laminar die casting, a comparatively low mould filling speed keeps the gases from being trapped. Die cast components are annealed as per a time-temperature profile, which depends upon the alloy as well as dimensions. This way, a homogeneous hardened solution is produced in the components.
After a certain amount of annealing time, they are quenched in water as well as in some cases, re-annealed one more time. This procedure is known as “T6 heat treatment”.
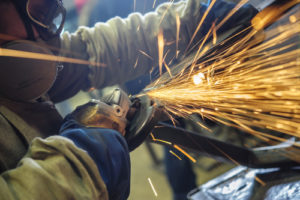
Die Casting Process
Following the first annealing procedure, the solid solution gets supersaturated with the alloying atoms. A longer components’ ageing at room or elevated temperature has the effect that excess alloying atoms spread out from the said solution, build up in certain boundary zones as well as form inter-metallic compounds.
In the precipitation hardening process, the microstructure’s hardness as well as mechanical strength increase, so those of the cast components also do.
Slight Grinding as Well as Other Surface Treatment Processes
A work piece’s surface is especially subjected to external sources of pressure, like, wear and corrosion, for instance. Many processes for the treatment like powder coating, galvanic coating, and slight grinding are offered in order to refine castings’ surfaces with a view to their next purpose or in accordance with aesthetical aspects.
Slight grinding is very often used for the components. The functional principle is the components are filled to vibrating tub where the parts come into contact shakingly with abrasive grinding chips aided by aqueous substances. The components are deburred subsequently and their edges are rounded off. This process can be performed relatively easily, necessitates short processing times, as well as produces a top surface quality.