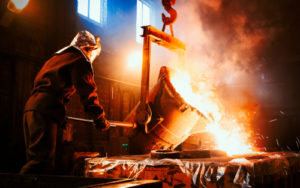
Melting Furnace Types
In metal casting, the required heat to be exerted to the metal so as to reach its melting point is applied through the furnaces. A furnace is used to melt the metals in initial stages of the metallurgical process. There are different types of melting furnaces used in casting, and each furnace uses various technology. Foundries design the melting furnace in a particular way so that it consumes less heat and fuel as possible in order to melt the metal.
Cupola Furnace
This type of high, cylindrically shaped furnace is one of the oldest melting furnaces used in casting applications. The inside of the cupola is lined up with clay, bricks, or blocks, that protect the inside of the furnace from higher levels of heat, abrasion, and even oxidation. For melting the metal, foundry operators put several layers of ferroalloys, coke and limestone in the furnace. The sedimentary rock used as a construction material will react with the metal, which makes the impurities in the furnace to float up to melting metal’s surface.
Induction Furnace
As the name implies, these melting furnaces use induction technology with alternating electric currents to apply the required heat to melt the metal. The electric furnace used for melting metals makes the process energy efficient when compared to other types of melting furnaces. Most of the global foundries use induction furnace instead of the cupola to melt brass or cast iron.
Besides that, induction furnaces are preferable for melting an array of metals including steel, iron, aluminum, and copper. Since it uses induction over combustion, the thermal energy required to melt the metal will be adequate; thus, it will cost savings to the die casters. The furnace can melt from less than 1 KG range to up to 100 tons.
Open Hearth Furnace
Foundries use the hearth furnace to melt nonferrous metals in smaller quantities. It uses atomized heavy oil or natural gas in order to create heat with which to melt the material. The open hearth process is also used as means to raise the heat inside a metallurgical furnace that makes use of the waste or unused heat forced out of the furnace. The waste heat then redirects furnace fumes via brickwork that forms a checker. The hearth furnace is used primarily in industrial applications as an oxygen-based furnace or an electric arc furnace.